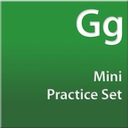
Glendale Gloves is a manufacturer of baseball gloves, which it sells directly to wholesalers and national retail outlets. Glendale Gloves operates in a job-order costing environment employing JIT inventory practices. Direct labor is charged directly to the individual job cards (sheets) with an automatic charge for manufacturing overhead at 80% of direct-labor dollars.
Glendale Gloves uses process costing for its product-costing system, and has two major production departments: (1) Cutting and Shaping Department and (2) Sewing and Packaging Department. Glendale Gloves applies ‘just-in-time’ inventory practices to all of its direct-material inventory purchases.
Students are required to (1) enter daily entries for the last month of the third quarter of the fiscal year, and (2) complete departmental production reports, including the computation of equivalent units of production when units are transferred from one production department to a subsequent production department and when units are completed.
The journal entry to record the Cost of Goods Sold is automatically performed by the program whenever a sales transaction is recorded. There are other time-saving features such as a repeat-date function, an automatic balancing of the journal entry at the last credit entry, and the program’s automatic recording and posting of the closing entries.
Each week of the last month of the third quarter is divided into Modules. At the end of each module, students are required to print a trial balance and check the accuracy of the account balances against a Check It Out Box, which contains the correct balances of several accounts that have significant activity, or no activity, during the data entry period of the module. Students will use their general journal and the check figures to verify their work, and when necessary, locate the error and correct it. At the mid point of the project (end of Module Two), students are required to print several documents and answer the Mid-Project Evaluation questions. After completing the fourth module, students will record the adjusting entries and close the under- or over-applied balances of the manufacturing overhead accounts to the Cost of Goods Sold account. After the financial statements and other selected documents are printed, students are required to answer the Final Evaluation questions which are designed for students to analyze their work. The Mid-Project and Final Evaluation are graded electronically and can be submitted in printed form or e-mailed to the instructor. Instructors can require key documents, such as the income statement, to be attached to the graded questions.
Included within the recording of direct material and manufacturing overhead transactions in the manufacturing accounts are:
• the allocations of telephone, supplies, insurance, and property taxes expense to the manufacturing process
• recording the accrual and payment of direct labor, indirect labor, and offices wages and salaries
• payments of accounts payable, credit and cash sales, and collections of accounts receivable
• payments of short-term and long-term obligations and sale of obsolete manufacturing equipment
Students are required to periodically reconcile the difference between the balance of the subsidiary ledger for Job Cards and the Raw and In-Process Inventory general ledger account. Over- or under-applied overhead is closed to the Cost of Goods Sold account at the end of the accounting period.
The evaluation questions can be graded electronically and submitted in printed form or e-mailed for recording. Key documents such as the income statement and balance sheet may be attached to the graded questions.
Completion time is estimated at five to seven hours.